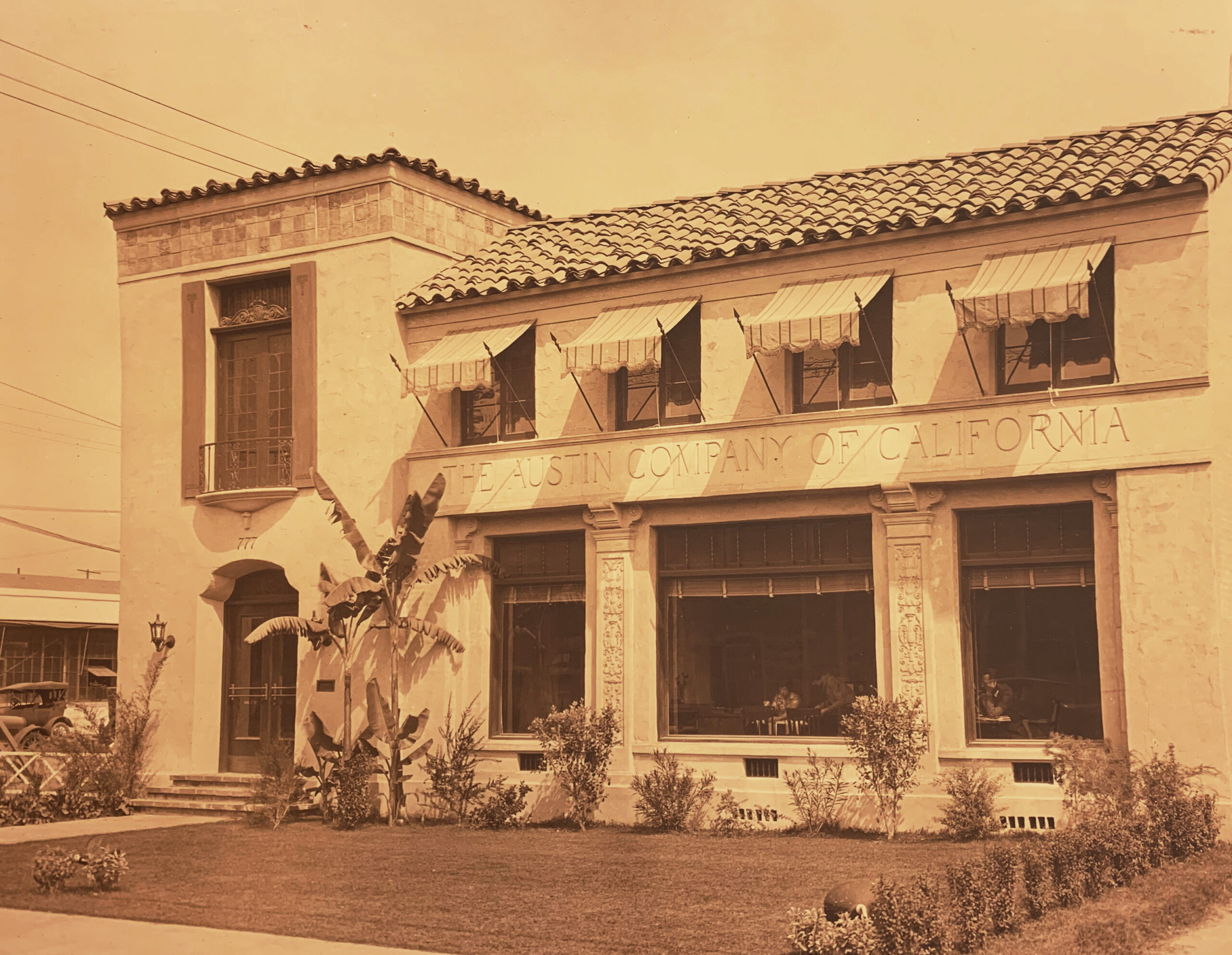
A retrospective of the first 100 years of work completed by Austin’s California Office.
This is the first in a series of monthly articles that will chronicle highlights of the first 100 years for The Austin Company’s California office. We begin in the 1920s as Austin lays down roots in California. Each month we will take you through another decade, highlighting projects indicative of the times. We will wrap up the series with a publication that includes these monthly features, along with other milestone projects – a chapter for each decade. We look forward to you joining us on this historic journey.
The Austin Company Opens its First Office in California
Records indicate that the first Work Order Number issued for The Austin Company’s new California office was on December 7, 1921, for a $20,500 project in Los Angeles. This equates to approximately $320,000 today (2021).
Four Work Order Numbers were recorded in December 1921. Twenty-two (22) projects were recorded in the year 1922 for a variety of companies, including the names of companies that few would recognize today; however, there were several projects for the Port of Los Angeles.
More than 50 projects were recorded in 1923, including projects for multiple ice cream manufacturers and the emerging industry of the times, petroleum-related companies such as Standard Oil Production Company of California, a company name that would ultimately appear in Austin’s active client list many times in the decades ahead. Also notable were multiple projects for the General Electric Company, as well as a project for The Austin Company’s new Los Angeles Warehouse. 1924 and 1925 records reflect a growing list of projects, including a project for Stauffer Chemical Company, a client who would return to Austin many times, continuing work for General Electric in Oakland, and the New Austin Office Building in Los Angeles.
Hollywood and The Motion Picture Industry
Cecile B. DeMille
1926 brought Austin’s first recorded work in the budding motion picture Industry for Cecile B. DeMille in Culver City, California.
Thomas H. Ince Studio, as it was originally known, was founded in 1918 by Ince, a silent movie actor, director, and producer, on land acquired by real estate developer Harry Culver. Ince had grand ambitions to create his own studio unique from all the others. Following Ince’s early death in 1924, his widow sold the property to Cecil B. DeMille, who renamed the studio to DeMille Studios.
DeMille undertook several large expansions, hiring Austin in 1926 to design, engineer, and construct Stages 2, 3, and 4, producing a few major box office hits, including The King of Kings.
Classics from Hollywood’s Golden Age were filmed at the studio, including Gone with the Wind (1939), and A Star is Born (1937). Orson Wells’ Citizen Kane and Alfred Hitchcock’s Spellbound were filmed at the studio in the 1940s. Over the years, the studio has had several owners and investors, including Howard Hughes in 1950 and Desilu (Lucille Ball and Desi Arnez) in 1956. The studio was also used for television shows such as The Andy Griffith Show, Hogan’s Heroes, Lassie, Batman, The Nanny, Scrubs, Arrested Development, and Cougar Town, among many others. The studio was renamed The Culver Studios in 1970.
Austin returned to the site in 1987 when the studio was purchased by GTG Entertainment a joint venture between Grant Tinker (Chairman and CEO with NBC from 1981 – 1986) who Austin had been working with while he was at NBC, and The Gannett Company. Austin prepared a master plan for the remodel and expansion at the studio, as well as the design of two new sound stages, adjacent to Austin’s original 1926 sound stages.
The studio is operated today by Amazon.
Mack Sennett

MGM (Metro-Goldwyn-Mayer)
Beginning with the early projects for Cecile B. DeMille and Mack Sennett in 1926 and 1927, Austin went on to design and construct over sixty projects on the MGM (Metro-Goldwyn-Mayer) studio lot in Culver City, just down the street from Cecile B. DeMille’s studio, including sound stages, support facilities, and offices. The MGM Studio is today known as Sony Pictures. The years 1926 through 1929 included a long list of projects for a wide variety of companies. Many of the names are for companies that few would recognize today, however, there are others that, like Austin, continue in business today and are well recognized, such as H. J. Heinz and Ingersoll Rand, as well as Universal Pictures and Metro-Goldwyn-Mayer (MGM).
Join us for more!
Join us as we continue our retrospective of projects completed by Austin’s California office. Next month we will explore the 1930s. The Great Depression rages through the United States, the aviation industry soars to new heights, and the broadcasting celebrates its golden years.